You need to pay attention to the inherent characteristics of biopolymers PHA/PLA materials when setting process parameters to realize better and more consistent outcomes. #sustainability
In the current legislative climate of bans on petroleum-based plastics and consumer requests for sustainable alternatives, bioplastics offer a unique opportunity. In prior decades, there has been significant resistance to bioplastics because of cost as well as unique, and often difficult, processing characteristics. Now, however, the development of many polyhydroxyalkanoate (PHA)-based resins — often combined with polylactic acid (PLA) — has resulted in bioplastic solutions that are well suited to current market needs. Bubble Film Machine
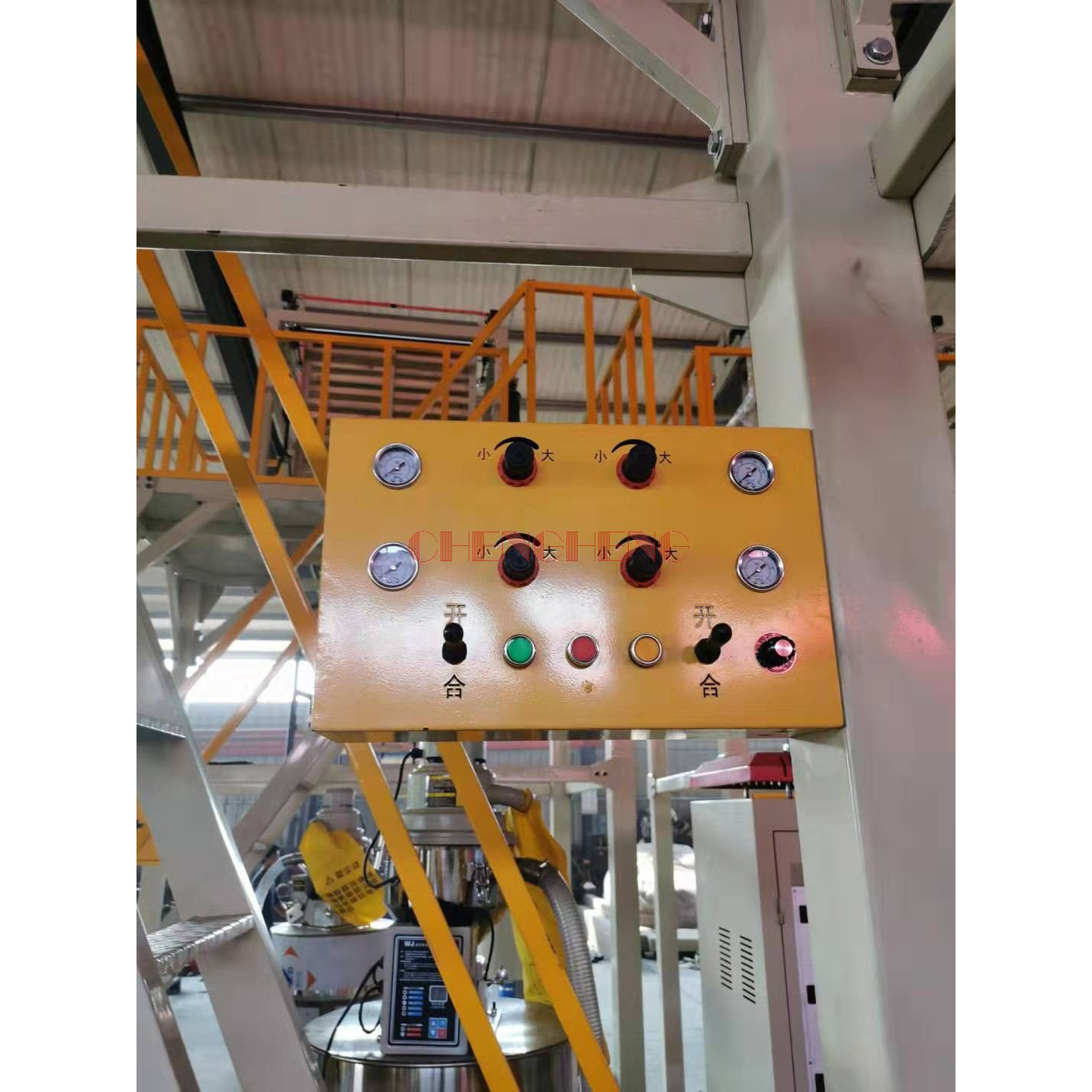
This is Part 2 in a series on PHA/PLA processing. Part 1 covers injection molding of PHA and PHA/PLA Blends.
PHAs are a naturally occurring biodegradable material produced via bacterial fermentation, similar to brewing alcohol. During fermentation, when nutrients and food sources are optimized, the bacterial strains start making and storing PHA as a food source, eventually producing a peak amount of PHA.
At this point, the PHA is separated from the cellular components and processed, resulting in a light, white powder that can be combined with other materials like PLA to produce processable and usable bioplastic resins. These materials are typically compostable in home and industrial environments, and degradable in soil and marine environments.
One of the opportunities to use PHA and its compostable characteristics is in blow-molded articles. The positive end-of-life scenarios offer one possible solution to the overabundance of plastic in the market. PHA can be blow molded into various shapes, sizes and designs for many applications, from personal use to food and drink storage.
To successfully extrusion blow mold PHA/PLA bottles you need to take heed of the unique processing charactertics of the material. Photos: Danimer Scientific
Recently, many processors have been experimenting with running PHA/PLA blends in their blow molding operations, with mixed success due to the blends’ unique characteristics. However, proper attention to the inherent characteristics of PHA/PLA materials when setting the processing parameters can lead to better and more consistent outcomes.
PHA can be blow molded molded into various shapes, sizes and designs for many applications.
When combining PHA with PLA, you will find that the processing requirements for the PHA will drive most of your processing strategies. PHA is hygroscopic and needs to be dry. It is sensitive to residence time and requires a warm (120-130°F) mold to crystallize.
At Danimer Scientific, most of our research effort has been with extrusion blow molding (EBM), which is the process covered here.
As noted, PHA is a hygroscopic polyester that will absorb environmental moisture. Having the material dry before processing will prevent degradation and melt thinning. A moisture content of less than 0.04% (400 ppm) is required. Recommended drying conditions are four hours at no greater than 170°F (80°C) with a desiccant dryer.
It is recommended to purge the machine completely with LDPE to remove the previous resin and, after cooling the extruder to the process set points referenced below, introduce the PHA/PLA blend. This procedure should get you into the production material without degrading the resin. PHA/PLA blends have an upper temperature limit of around 400°F and will rapidly degrade around this temperature.
Because PHA can degrade quickly under heat and shear, it is recommended that you purge fresh material forward anytime the machine is idled for more than five minutes before starting up again. It is not only the temperature of the melt that matters but also the residence time. High residence times will cause the material viscosity to decrease and can cause problems with machine startup.
At the end of production, the machine should again be purged clear of the PHA/PLA blend — using LDPE at process temperatures — before increasing temperatures to go to the next resin.
Once more, the PHA component will drive your temperature strategy. To achieve a stable and workable parison, you must keep your heat near the low end of processing temperatures for PHA.
The low melt temperature aims to achieve a parison with enough melt strength to hold together. You will find that PHA/PLA blends are sensitive to the smallest temperature changes, and viscosity will drop rapidly as melt temperature increases. We typically advise processors new to PHA/PLA blends to think of adjusting temperatures by two or three degrees at a time, not the usual five-degree changes.
While extruder speed is directly related to cycle time, it should be noted that PHA is a shear heating material similar to PVC (polyvinyl chloride). As production rates and extruder speeds increase, you will see temperature override in your extruder zones. If your machine has heat cool bands, you can employ those to keep temperatures inline or you can try to introduce some heat earlier in the extruder to reduce friction and shear heating.
It would also be helpful to look at your extruder screw design and avoid screws with higher compression ratios or very short, aggressive compression sections.
This area requires particular attention. The PHA component of the PHA/PLA blend requires a warm tool to promote timely crystallization. If you process into a cold tool at 40-60°F, the parts will come out soft and pliable and then, over the next 60-90 sec, become firm. What is happening is the part is crystallizing in your hand. The cold temperature is retarding the crystallization rate. When working with PHA/PLA blends, crystallizing and cooling are different. Parts can be cold and not crystallized.
The PHA component of the PHA/PLA blend requires a warm tool to promote timely crystallization.
To aid the crystallization rate, keeping the mold at 110-140°F (40-60°C) is recommended. The strategy is to get the mold warm enough to promote crystallization yet cool enough to enable part ejection and handling.
Another reason to keep the tool warm is that most blow-molded PHA/PLA blends will stick to a cold mold surface, making it difficult to eject them.
Cure time before packaging may be required for PHA/PLA blow molded bottles.
An important part of any blow-molding process is how you handle the parts once molded. The handling of parts made from PHA/PLA blends will become more difficult as production speeds increase.
As cycle and crystallizing times decrease, the bottles will become softer and easier to damage. It may require some engineering and automation adjustments to enable some post-molding cure time before the parts are bulk packaged.
You may also have to explore some forms of ejection and part holding as the mold opens to keep the bottles releasing consistently due to some variability in whether the bottles will stick to one side or the other or release cleanly.
Hopefully, this outline will provide some basis for developing a process for your parts. If you go at it slowly and methodically, you should be able to create a stable process and then improve from there. Remember that PHA/PLA blends are relatively new and different materials that require some new and different processing techniques.
About the Authors: Russell Mullins is Danimer Scientific’s special operations technical advisor and has more than 45 years of experience in plastics injection molding and product design. Dr. Karson Durie is associate director of Danimer’s facility in Athens, Georgia, and earned a Ph.D. in chemistry from the University of Georgia. Contact: 229-243-7075; russellmullins@danimer.com; danimerscientific.com.
Adding aPHA to PLA can boost a range of mechanical properties and expedite composting. Here are the details as well as processing guidelines for injection molding the blends.
Here are processing guidelines aimed at both getting the PHA resin into the process without degrading it, and reducing residence time at melt temperatures.
Beyond PET, PBT and their analogues, development of polyester chemistry led to unsaturated thermosetting resins, copolyester thermoplastic elastomers, liquid-crystal polymers and, most recently, biopolymers.

Monolayer Blown Film Line © 2024 Gardner Business Media, Inc. Privacy Policy [Log On]