A piece of manufacturing news from Tesla Motors caught our eye, that Elon Musk’s car company plans to die-cast major underbody structures — in effect the chassis — for its cars. All the ingredients beloved of the popular tech press are there, a crazy new manufacturing technology coupled with the Musk pixie dust. It’s undeniably a very cool process involving a set of huge presses and advanced 3D-printing for the sand components of the mould, but is it really the breakthrough it’s depicted as? Or has the California company simply scored another PR hit?
We produced an overview of die casting earlier in the year, and the custom sand moulding in the Tesla process sounds to us a sort of half-way house between traditional die casting and more conventional foundry moulding. I don’t doubt that the resulting large parts will be strong enough for the job as the Tesla engineers and metallurgists will have done their work to a high standard, but I’m curious as to how this process will give them the edge over a more traditional car manufacturer building a monocoque from pressed steel. The Reuters article gushes about a faster development time which is no doubt true, but since the days of Henry Ford the automakers have continuously perfected the process of making mass-market cars as cheaply as possible. Will these cast assemblies be able to compete with pressed steel when applied to much lower-margin small cars? I have my doubts. Automotive Interiors Tooling And Molding
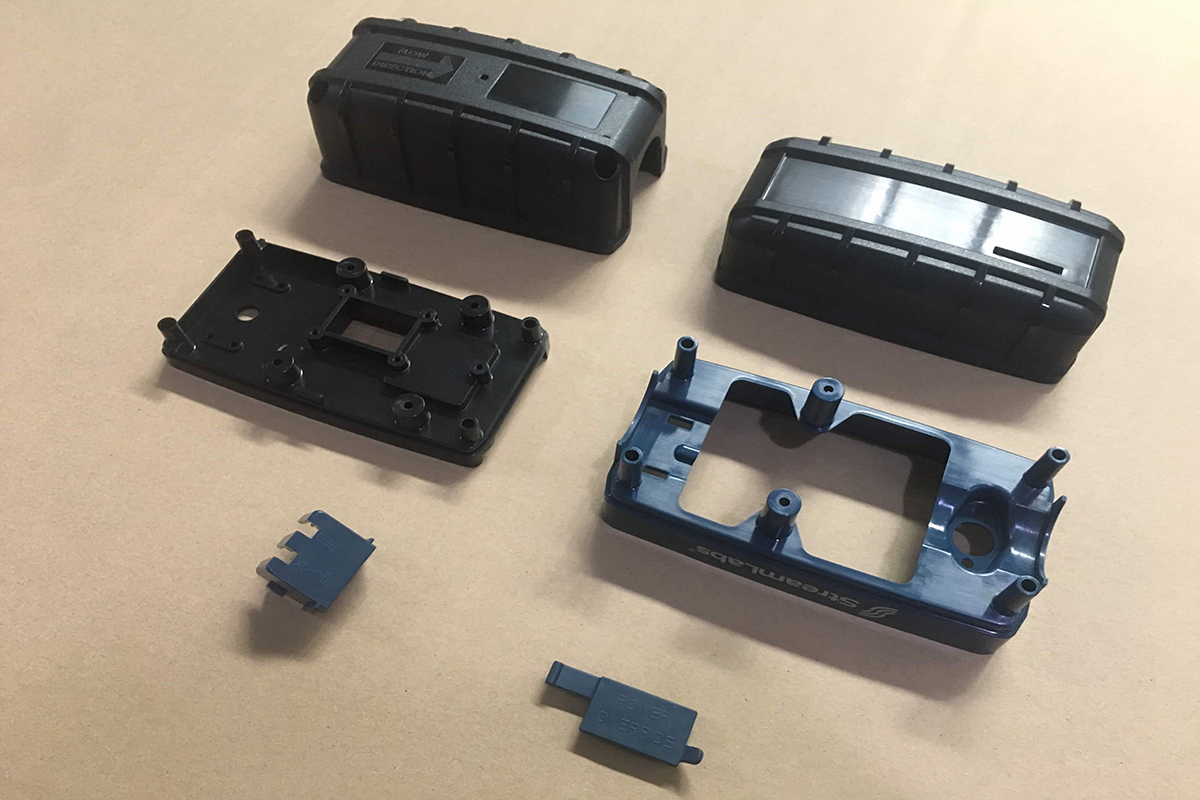
Aside from the excessive road noise of the Tesla we had a ride in over the summer, if I had a wish list for their engineers it would include giving their cars some longevity.
Header: Steve Jurvetson, CC BY 2.0.
Grown up version of a Hot Wheels car.
Can’t wait to see the bill when you need to replace it.
Cars are going to the cell phone model – pay a monthly subscription and throw it away every two years after the “manufacturers” send an over the air update to brick your vehicle.
It’s proven technology. Gummy bears are made that way as well.
They might find out that like early jet airliner designers structural fatigue calculations can have an error margin of 900% in practice.
Anyway, thought something else had cast subframes 20 years ago, can’t remember what.
Ford Falcons and Holdens in Australia, Triumphs (sedans and sports cars) from England – plus lots more I suspect. It’s not exactly new at all.
ummm, what holden or ford has a diecast subframe in Oz?
Falcon AUII (and later I’m sure) , alloy front sub frame that holds engine, steering rack andlower mounts for the front suspension. This bolts to longitudinal steel rails and a steel floor and sills. My understanding is the biggest issue for alloy/aluminium things like heads and engine blocks can be porosity and allowing the item to cool too quickly and hence shrinkage and cracks. I also understand foundries also apply a vacuum to minimize the porosity issue.
Diecasting is like injection molding, except with metal.
It’s very new at this scale. There have been previous diecast body parts, but not many, not until recently and not any near this big.
Aluminum has some bad fatigue characteristics. If your car has Aluminum suspension components, those are wear parts. When the bushings are roasted, you need to replace the whole link. Old collectable aluminum cars like AC cobras are like glass at this point. The metal no longer bends, it just cracks.
Since many of the other manufacturers have indicated that they are heading that way, it sounds as if they think it is a good idea.
And if you take a look at the number of welds on your car, you’ll understand how many pieces are actually in today’s vehicles.
Speaking to the point of parts count and welding, I have to wonder how this will affect unibody construction in commuter/consumer vehicles.
I’ve always been a proponent of body-on-frame design for the sake of modularity.
They’re talking about casting one single subframe for the entire car, from rear to front. What this means is that almost any accident involving the suspension attached to this subframe will total the car. Insurance companies will love that, I’m sure this won’t massivly raise the cost of insuring one of these.
Just because it was made as a single part doesn’t mean the repair is going to be impossible, or even difficult. Assuming it actually bends or breaks in anything but the most excessive accidents, the bits that take a pounding even in normal accident free use are bound to get those subsections available as a section in the same way you can get body panel rebuild sections etc. Maybe it will be as a bolt on, maybe as a weld/braze on but assuming they made the cast frame with enough margin on the mechanical properties to be able to survive the road at all it shouldn’t be that hard to repair.
The insurance companies love writing off barely damaged vehicles anyway, and this isn’t likely to change that.
Considering many car body shops don’t even dare to work on less fragile (stamped or pressed) Al parts, one should not expect Al die-cast part repair to be a common thing. In fact, it’s for a good reason: Most casting Al alloys tend to crack past their yield point, and weld very poorly because of their Si and Mg content. And because of the large cristalline structure, a bent cast Al part will develop internal (invisible) micro-cracks, weakening the part without noticable external signs.
For this reason, In Germany (and probably other countries), repaired Al wheels are illegal to use on the road. Not sure about the legality of Al frame repair though.
So yeah, it is to be expected that a seemingly minor impact will result in a write-off when moving to a single-piece die-cast chassis.
So much for the sustainability of these electric cars…
Really depend on the alloys used etc, so I can agree its possible, I just don’t think it will happen.
For something like a frame to the whole vehicle I’d expect an err on the side of caution so tis rather harder to break in the first place. As warranty failures for the core frame of the car are going to be way way more expensive to deal with than a later stage of production part failing, and create more media frenzy.
And similarly to err cautions on the material selection so that giant frame that didn’t quite cast well enough can be relatively easily reworked over scrapped – this is a large scale where having to start again every time there is a minor flaw would be excessively expensive compared to a small scale casting like a wheel, and the risks of allowing though lower quality casting are too high when you are about to add thousands of other parts and heaps of value to it as well.
Though I may be expecting too much sanity…
There are few choices for diecasting alloys. None are durable.
They aren’t going to rework these parts. That would defeat the point of diecasting. Perfect or back to the melt.
One problem is cast in internal stress. For wheels they freeze off the metal from the edges in, so the stress is a preload to prevent metal flex and fatigue. Why welding on aluminum wheels is such a bad idea.
The fact is that replacement battery packs aren’t going to be common. Teslas have design lives equal to one battery pack life, same as a new German gas powered car. Like bic lighters.
HaHa with the scale of this casting I’d be surprised if they didn’t rework some of them – though that will depend on exactly what materials are in use etc. But when the casting has a huge investment in time (even if much of it is time no human has to be actively employed for), space (as all those processes that take no man hours go on) and energy to get that far employing one or two people with the skills to rework the near misses makes sense – quicker and much cheaper than starting from scratch again.
I tend to agree. But in terms of sustainability I guess the batteries can be reused and the cast can be melted and then the material be reused. And more of such recycling should be doable. Still not good for the buyer though.
The world has moved along. Body shops now have the skills to work on aluminum parts. Granted ‘replace the panel’ is the standard for any material.
In 10-15 years, body shops will fully understand repairs on cast parts. I’m betting it will still land on ‘no’.
You can already see the effects of unrepairable cars on insurance rates. Why BMWs cost so much to insure. But egos are gonna ego, so they continue to sell.
I saw a car youtube channel where some twit was heating and beating the diecast aluminum fender frame brace of some totaled Italian trash. Hopefully he was doing it for views and will part out the car, but I doubt it. My second hope is that it will be bought by a typical Ferrari owner. Who can’t drive and will just putt around in it, impressing his fellow idiots.
With body on frame construction and the potential simplicity of EV chassis, wouldn’t full frame replacement become more of an option if Tesla sells them at reasonable cost.
“if Tesla sells them at reasonable cost”!!! Lol.
Servicing a Tesla costs $2k when I asked. The salesperson wouldn’t comment on replacement parts costs either.
Aluminum can be tig-welded. It can also be repaired with carbon fiber. Both methods probably require more talented professional workers than ordinary car repair shop has. Carbon fiber needs to be insulated from aluminium to prevent corrosion.
An auto body shop would never tig weld a subframe or, heaven forbid, patch it with carbon fiber for one simple reason: liability. An insurance company is unlikely to approve such a repari in any case.
No chance man. No way.
Cast Alu is a royal PITA to weld in a mechanically solid way due to included garbage in casting alloys, most places will weld it but warn you it might fail during or after the welding. This will be a replace-only and and scrap the car essentially. Right now, in the UK, anything that damages the structural frame of a body-on-frame, where the manufacturer doesn’t provide approved welded repair processes, writes the car off.
I welded my aly water pump casing after it cracked due to a stress fracture (dealer-mounted supercharger bracket).
It’s still going strong 10 years later and 70,000 miles. But – I did add lots of extra material.
Don’t worry, it’ll increase the price of insuring everything else because of liability coverage.
there’s a lot better alternatives, that’d I rather not share as I’d rather Tesla as a company and Elon as a “human” f*cked off [to mars OR and died], but the more I hear about what they do in their manufacturing, it really seems they refuse to learn from the hard learned lessons of actual car companies that have tried all that and sundry..
To be fair, SpaceX also refused to learn the hard learned lessons of actual space companies.
Oh come on. SpaceX deliberately ignored the conventional wisdom and look at what it’s achieved. Actual space companies said you can’t land booster rockets and you should never reuse them. So much for the “hard learned lessons of actual space companies.” You don’t know what you’re talking about. SpaceX has successfully launched more missions than everyone else combined.
Doesn’t the Soyuz system have more launches?
Soyuz is not a launch system though, is it?
Wut? Everything they have done was based on gov’t research and proofs-of-concept. Their innovation comes from the benefit of decades of tech development and cheaper material processing. Landing boosters had been done – it wasn’t economic in the 90s.
Just like edison, musk simply bought other peoples ideas, fired anyone who told him no, & plastered his face on them.
Everything is based on gov’t research and proofs-of-concept. Nearly every company with a revolutionary product has been made by grads coming from programs with federal grants or similar. And all those programs are built on academic and scientific collaboration. That doesn’t make the spin-offs’ work any less exciting
If SpaceX hadn’t made the Falcon 9, we’d still be stuck with the same couple of stodgy old launch providers with their monopolistic prices and painful launch cadences, and who knows what our human spaceflight capability would look like. We’d probably have something, but it’d probably be monumentally expensive.
It’s possible that some of the smaller launch providers that have popped up since would still have come around (or similar companies), but I really think that the Falcon 9 showed that making an alternative to ULA was possible.
I’m not saying that your last sentence is incorrect, just that it isn’t mutually exclusive with SpaceX having done stuff that would have taken at least another decade or two (at least in my view, just look at Blue Origin) for others to get around to doing.
To be fair, SpaceX launches entire “reusable” rockets built to match a failed Soviet model (specifically on the birthday of a then-dictator, mass-murderer, war-monger and ex-employer of W. v. Braun) from a launch pad hardly fit for that purpose just to destroy both the rocket and the launchpad and contaminate several square kilometers of wildlife refuge with the resulting debris. As for the rocket, not even the effing self-destruct systems worked.
> refused to learn the hard learned lessons
Maybe more people should listen to the wise words of successful entrepreneur, engineer and explorer S. Rush when he said “safety is just pure waste”.
Or to actually be fair, they have launched 60 Falcon 9’s and 3 Falcon heavies as of September this year, with a better than 100% first stage landing rate thanks to the triple booster heavies.
Or you could just throw around utterly nonsensical connections to Nazi’s and Soviets….
A “better than 100% first stage landing rate” implies that more first stage rockets landed than were launched. Either your grasp of math is tenuous or you work for Tesla’s PR department.
@Bob Reed 3x Falcon Heavy -> 1 launch, 3 1st stage landings
Triggered much are we? Plenty of other people also share that particular birthday.
Maybe you missed the fact that a certain group of society celebrate the 20th of April because of a certain plant, and Elon happens to find that day (in US backwards date order) amusing, as do many others.
I guess you believe he set the price he’d buy Twitter at based on somebody’s birthday too.
Exactly. And on the inaugural dates for various things scheduled on a dictator, mass-murderer’s birthday topic, I’m sure I could find, if I wanted to waste my time, all kinds of things scheduled on Stalin’s, Mao’s, and Pol Pot’s birthdays.
“safety is just pure waste”
Kind of depends on whether you are a passenger or a spectator, I would think.
Next they’ll be building carbon fibre deep sea subs
If they do, they’ll take into consideration previous attempts and failures by others.
It’s the least funny (thus least important) thing about him
Spook Internet getting stolen out from under them has been so good
Pushing too far? Quite possibly: https://www.autoevolution.com/news/new-images-and-video-confirm-austin-made-tesla-model-y-has-cracked-front-casting-220165.html
they should have replaced his car as fast as possible,,
This is terrifying but apparently par for the course when it comes to the sloppy way Tesla deals with QA. A cracked frame and a missing brake fluid cap (in two different cars, but still) does not sound like safe-to-drive, yet that is what Tesla representatives told the owner.
It is at least plausible that a small crack is entirely safe, the part may have so much structural margin because its easier to make it that way to be safe with heaps of cracks and bits missing… But I do doubt it in this case, and its rather poor form to forget the brake fluid cap enough for people to notice. The odd error will always sneak through, even with great QA, but it should be only the odd error, and each one really rare in its own right, say one in every 100,000 at worst. As then you only get a handful of folks that will ever find they got a factory error, and that particular error is so rare it doesn’t get noticed as a common failure.
A die cast magnesium sub frame would make for a truly light weight and completely inextinguishable EV. Interior parts made entirely of Trinitrotoluene are another hot development.
I vote for the magnesium-frame offering to be named the Tesla Inferno GTi.
I feel like die cast of steel alloys would be more energy intensive than pressing steel. Sure you can do some really complex shapes with a die cast, but even if you have to press a few different pieces then weld them you’ll still have an energy advantage.
Steel? Die casting is almost all aluminum-nickel alloys cooked up for the purpose. The molds are steel.
Fatigue life will be an issue. Cracking will happen and won’t be fixable. Good news! Battery will be dead long before that.
Tesla is using aluminum, not steel for this frame.
They’re not doing this for the energy advantage, AIUI. They’re doing it to reduce the number of production steps, i.e. save manufacturing time.
Ahh, another example of the Silicon Valley mantra ‘move fast and break things’ though in this case the consequences of a fast moving 2 ton dinky toy breaking are just unacceptable.
Only for those with enough spare cash to burn. Mere mortals like myself would not care.
Regardless how well a metal part is cast, it will still need tempering/annealing and further machining to some degree to meet exacting tolerances and special features (threads etc).
X-ray inspections to move on the production line. Multi-part castings make sense from a repair point of view as dinging a front end could result in a total loss otherwise.
In conjunction with self-driving, the safety benefits may well outweigh the implied risks.
New or repurposed manufacturing methods always cause naysayers to scream about the past, without fully accepting that visionaries may have a completely different take on the technology.
It’s gonna need nuclear derived energy to make the process ‘green’ anyway.
It might be fine for the smooth highways and tiny countries in Europe but I wonder how it would stand up to some of the potholes and corrugations in regional roads here in Oz. We have some doozies, I’m sure there would be similar ones in the boonies of the US.
A casting can be strengthened by shot-peening but I don’t know if it would surpass the longevity of a stamped/forged steel chassis. But I am sure Tesla knows what they’re doing.
Interesting fact about cast-chassis vehicles, back in WW2 Australia was the first country to produce a battle tank (Sentinel AC1) that had an 100% cast 1-piece armour steel hull that was not achieved anywhere else at the time.
Really is going to depend on just how good your frame design, casting alloy and process are. It might be in practice able to take anything remotely sane even from awful road – using a bit more material and making your single part cast frame excessively sturdy is probably a winning move for the company really. Means even a slightly poor casting will be good enough to use, so higher yield even if the part costs more than it absolutely must in materials. 99.9% of customers will never look at this part anyway, so it doesn’t have too that perfect.
Though only time will tell, and being Tesla I’d be more willing to be on failures than excessive quality – they do seem to push the boundaries quite aggressively on new ideas in a way most companies just won’t. After they have been making them for a few years perhaps the process will be refined and reliable, but I’d never want to have my life on the line as the guinea pig for a Musk company. A bit of money for something like Starlink if I had need of it in those early days sure – its only money, as long as you have enough for the basics wasting some on a failed idea doesn’t matter. But if I have to trust in a new, novel, re-invention type idea from them while risking anything that matters much to me I’ll pass, not many company out there now that would actually gain that level of trust either though…
This is going to have the same problem that “unibody” construction has. Any deformation as a result of a collision(even in a body panel in the case of unibody) is going to effect wheel alignment – sometimes in counterintuitive places – and decimate the value of the vehicle. Fixing this would involve applying forces to the entire structure to bring them into spec while the effected panel is repaired. Just not cost-effective or even practical.
I had this happen with a Neon that I hit a deer in… there was only a small one-inch dent in the fender panel but somehow that bent the frame in an “irreparable” way.
Even if you could apply coordinated forces in 1000 different places, there’s still hysteresis to contend with.
Maybe get robots to do it.
https://youtu.be/dCXu8Ju_fdY
Neons/PT cruisers where built unfixable.
Anything can be fixed. For those two, step one is ‘melt car’.
They’re trying to save money like this, but think that you need a CAN bus for every last electrical aspect? Does it really require a computer to operate a tail light? Switch, wire, LED, done. But yeah, make the metal parts like a toy, that makes sense.
By now, I’m sure the die is cast. B^)
can bus saves on weight and cost of wires
If water infiltration into a tail light kills the whole engine, you should defenestrate some engineers as an example to the others. There is no sane way to argue against this. Can bus is garbage.
Switch, additional power cabling, additional dash material, and reinforced mounting points across an entire car are more expensive than a single old, cheap computer with data cabling. Is it better? In some ways yes, in some ways no, but either way it’s cheaper.
Cheap trash future. It cracks me up that some people still think we’re gonna explore space. Lol!
as a metal worker who does one of a kind custom work,design and build,I will point out that higher parts count=complexity=higher production times and costs. if you put your hand on a solid object and relax a bit you will feel a faint vibration,thats old Ludd spinning in his grave at 50 000 rpm larger complex metal structures are going to be incorporated in most consumer goods,and quality will go up and costs down stuff like hand made furniture and clothing,musical instruments,will always be in demand,and many many other services and trades will be very difficult to automate and optimise, so a balance will be established but the days of factorys(and offices)with thousands of workers in one big building is numbered and I say good ridance to them
“but the days of factorys(and offices)with thousands of workers in one big building is numbered and I say good ridance to them”
I think that’s called…Amazon.
Ludd wasn’t against new innovation, he was a labor leader looking to secure his work. And you might live to see that attitude come for your own bread and butter too.
This sounds like something that has been around for at least 12 years. ExOne make the machines, and we have one at work for making prototype parts in iron and aluminium. https://youtu.be/Z8MaVaqNr3U But ours is only big enough to make engines, not entire cars. And it _still_ takes an overnight run to print the mould. I can’t see this scaling to make production vehicles, especially given that each machine costs a few million. I guess if you were setting up a print farm of a few hundred printers the cost would come down, but enough?
3D printing large volumes is just inherently fairly slow, if you want decent resolution.
This sounds like a great idea if you aren’t at all sure what your part needs to look like. Keep it perpetually in the rapid prototype stage, and everything you screw up in the first set can be fixed in the second set, etc. over the life of the production. It doesn’t lend itself to a consistent product or a robust supply line for repair parts, but I think Elon sees those issues as tomorrow’s and someone else’s problem. On the other hand, you could take the extra time to bring your product to market, iron all the issues out using rapid prototyping, and then have the dies made so that parts come out of the press chunk chunk chunk one per second all identical, all functional, and all capable of fitting every car they’re supposed to fit.
Probably just me but when I read (an) article on this earlier this week I was left confused about several things. It seemed to mention “floor pan” so I could not tell if they were talking about die casting the floor pan in one piece or if they were talking about casting a stamping die to stamp the entire floor pan in one piece (vs traditional subtractive machining). Never seen the underside of a Tesla! Kind of surprised they aren’t stainless steel. How are they holding up on northeast us states that pound down road salt in the winter?
They don’t care, these are California/Austin/New England cars. Know your target demographic.
Sandy Munro seems to be a big fan of castings: https://www.youtube.com/watch?v=CeL82DX-BnQ
And coincidentally The Autopian have a dive into the whole thing too:
https://www.theautopian.com/how-tesla-made-gigacasting-the-most-important-word-in-the-car-industry/
More Than 5 years ago, I Admired the casting that carried the drive unit. Very Impressive says I. This Video Is Two Years Old. Speaks to the Frame. https://www.youtube.com/watch?v=rsBbt3TxKGg
Please be kind and respectful to help make the comments section excellent. (Comment Policy)
This site uses Akismet to reduce spam. Learn how your comment data is processed.
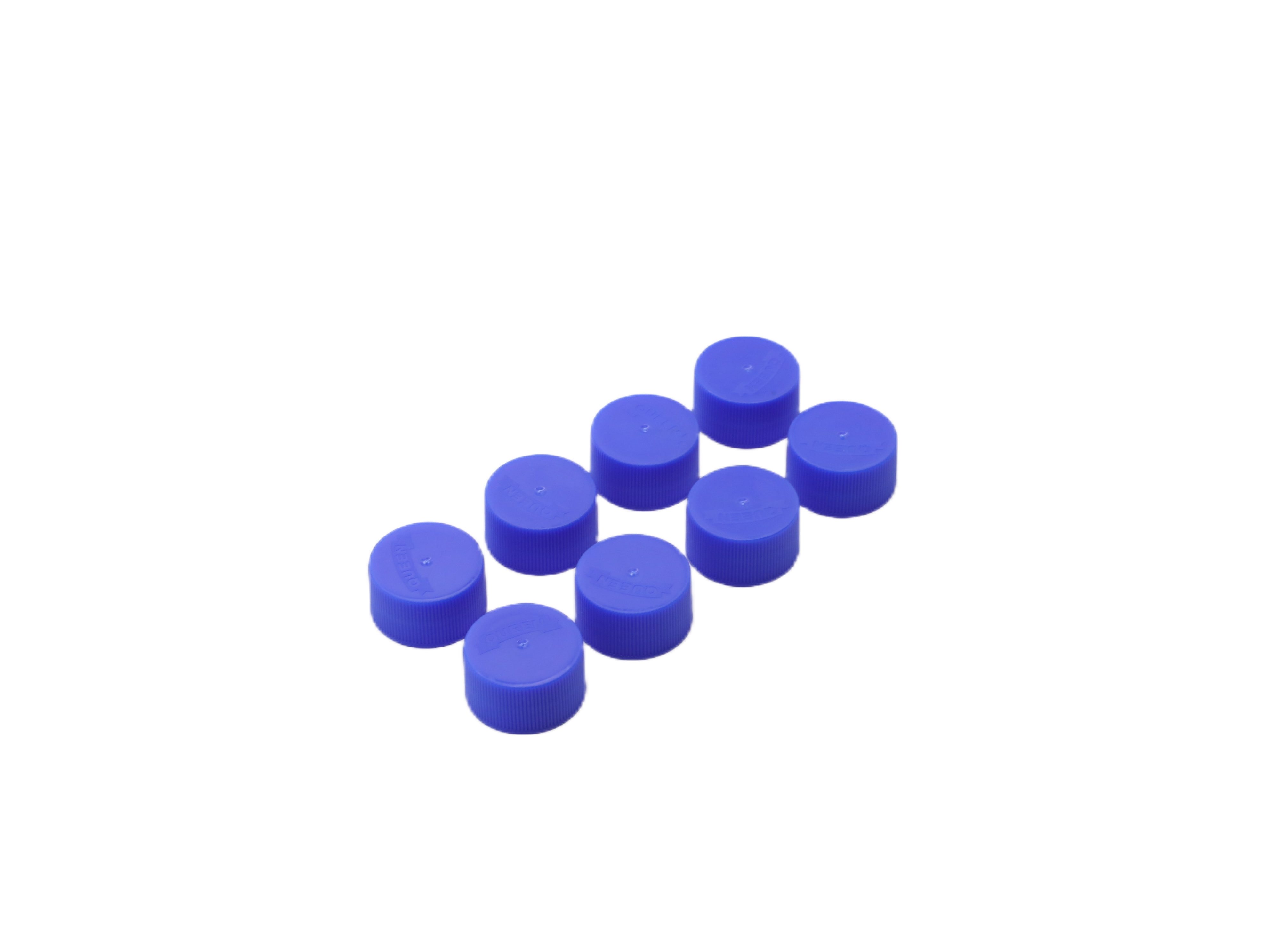
Good Price Die Cast Mould Manufacturer By using our website and services, you expressly agree to the placement of our performance, functionality and advertising cookies. Learn more