Pat Manley and Oliver Ballam demystify boat electrics and explain how to use and make secure electrical wiring connections
Protecting a connector with spray grease. Credit: Fernhurst Credit: Fernhurst End Terminal Block
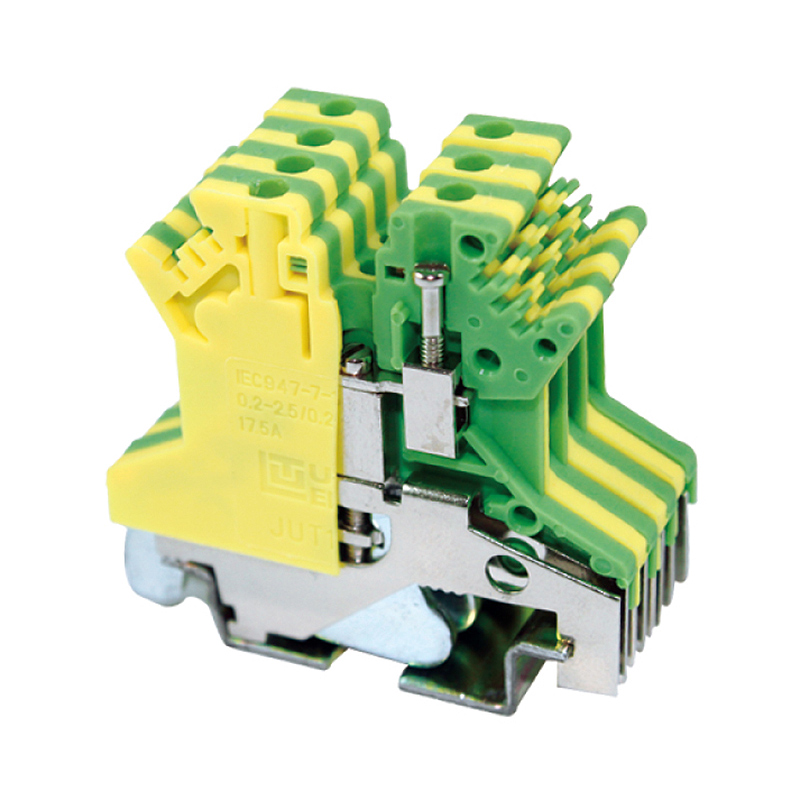
How to make and use electrical wiring connections for boats
Connections are the heart of the electrical system and if we’re not meticulous in making them, they can be its downfall.
Corrosion is the enemy of all cable joints on a boat. Any exposed cable joint should be protected using silicone grease.
The connection may be a joint between just two wires or a joint between multiple wires.
These connector blocks have a clamping leaf which is pushed down by the screw to hold the wire. Credit: Fernhurst
There are a number of different ways to make the joints and you need to consider if the joint is to be permanent or if it needs to be undone from time to time.
The strongest permanent joint, having the least electrical resistance, is a soldered joint made on new, bright wire.
Electrical wiring connections: Without a clamping leaf, as here, there is a risk of breaking the strands of wire. Credit: Fernhurst
However, a soldered joint may melt in the event of a short circuit. Signal wires are small in diameter because they carry a very small current.
They are typically used for instrument wiring and are fairly fragile, so they need special consideration when being joined.
Alternatively there are Wago blocks which don’t use screws, but have a spring contact. Credit: Fernhurst
There are two schools of thought on whether the end of a wire should be ‘tinned’ with solder or not.
Soldered joints use a flux to remove oxidisation from the surfaces to be joined.
Marine grade ‘bus bar’ connector. Credit: Fernhurst
This flux may be acidic and can cause subsequent weakening of the wire.
On small-diameter, multi-strand wire, stresses can be induced by movement at the junction of the soldered wire and the unsoldered wire.
Electrical wiring connections: Multiway connector block. Credit: Fernhurst
The screw of a screw terminal and the crimping process are both unable to ‘squash’ the soldered part of the cable and joints may be less secure.
Most technicians recommend that the ends of the wires should not be soldered.
Also known as ‘chocolate block’ or ‘strip connectors’.
These allow joints to be made and remade as required. Select the appropriate-sized terminal block for the wires to be connected.
Using a wire stripper, remove just sufficient insulation to fit into the terminal.
‘Chocolate block’ connectors – no good for damp places. Credit: Fernhurst
Insert the wire into the terminal and tighten the clamping screw, ensuring that the screw presses down on the centre of the wire’s core.
‘Chocolate block’ connectors are not ideal for use on a boat, unless in a very dry area.
If used, both the wire entries and screw heads must be insulated against moisture ingress with spray grease to prevent corrosion of the cable.
Use crimp eye terminals – no more than four to a single screw or post. Credit: Fernhurst
Do not try to keep moisture out by wrapping it with self-adhesive electrical tape.
Connector blocks or strips should be made from marine-grade materials, which rules out those bought from the local car shop.
Non-ratchet crimping tool. Credit: Fernhurst
If they’re to be used with small-diameter signal wires, such as those used for instrument connections, they should have a clamping leaf to hold the wire, otherwise the wire’s strands may be broken as you tighten the securing screw.
Connection of signal wires is probably the most useful application on board for ‘choc-block’ connectors.
The better ratchet crimping tool. Credit: Fernhurst
For power connections, marine-grade ‘bus bar’ connectors should be used with crimped terminals on the wires, preferably self-sealing ones.
Never wind a wire around a bolt and screw the nut down on top of it – always use a crimped eye terminal.
This is to ensure proper contact and security of the joint. Do not fit more than four eyes to a single screw or post.
Crimped connectors come in a variety of shapes and three different colour-coded sizes.
Using an oversized connector will make a weak joint. Using an undersized connector will mean not all of the strands of the wire will fit into the part which is crimped, making this a bad connection.
So you need to use the correct size connector for the wire being connected.
Crimping tools and connectors are available cheaply from car shops.
The much better double crimp (left) and the cheaper single crimp (right). Credit: Fernhurst
The connectors may be made of steel and/or the metal will be too thin, preventing an adequate crimp pressure.
Most of these are a single crimp, meaning they have one metal ring which is crimped onto the conductor.
The better, more expensive, crimp terminals have two rings – one crimps onto the conductor and the other onto the insulation to give more support to the joint.
The cheap crimping tool will not allow sufficient pressure to be applied, potentially allowing the wire to pull out of the terminal.
Pat Manley and Oliver Ballam demystify boat electrics, starting with switches and relays
Even when you’ve done all your normal pre-departure checks, sometimes the engine still just won’t start. If you have ever…
PBO reader John Anderson writes: “I have the mast out of my 30 year old Malo to solve an in-mast…
Ideally, use a ratchet crimping tool, which, although more expensive, will make a secure joint.
This robust tool exerts sufficient force to make a proper joint on any size wire that it’s designed for.
You use a repeated squeezing action and continue until the tool automatically releases at the correct pressure.
It has three anvils, each of a different size. Each anvil is colour-coded − red being for the smallest crimp, blue a mid-sized one and yellow the largest.
The ratchet crimping tool’s anvils are matched to colour-coded crimp connectors, each of a different size and designed for different-sized wires, NOT the colour of the insulation!
You use the red anvil for red connectors, etc.
Spade connectors – male and female to fit into each other. Credit: Fernhurst
These come in male and female and can be fitted to the ends of wires so that the wires may be disconnected and remade as required.
Bullet connectors – male and female to fit into each other. Credit: Fernhurst
These are for attaching a wire to a screw, bolt or post and come in various hole sizes.
These are tube-shaped connectors with two crimps for joining wires in-line.
They typically consist of a metal tube that’s usually encased in an insulated covering.
All these connectors are available with a heatshrink sleeve (second), which helps waterproof the connector, or not (first). Credit: Fernhurst
All of the above will be available in heat-shrink variants – where the plastic outer sleeve is replaced by a heat-shrink sleeve, ideally with adhesive lining, which helps to waterproof the connector.
1. Put the wire in the stripper jaws – some stripper jaws have notches suitable for different wire sizes; others automatically close to the correct diameter.
2. Strip the insulation from the end of the wire.
3. Insert the bared wire into the crimp connector.
4. Choose the crimp tool aperture for the correct size – in this case, red.
5. Insert the crimp connector into jaws of the crimping tool.
6. Close the crimping tool jaws around the crimp terminal.
7. Squeeze the crimping tool until the crimp is correctly squashed.
8. Release the handles and check the wire is held securely in the crimp.
1. Place the first wire in the stripper’s jaws.
2. Remove just sufficient insulation so the wire will go into the terminal AND the insulation will be covered by the terminal’s own insulation.
3. Insert one wire into the terminal. You may need to twist the stands very slightly so they stay together and go into the terminal more easily.
4. Push the wire fully in, so there is no bare wire showing.
5. Insert the terminal into the crimping tool.
6. Squeeze the crimping tool to crimp the wire in place.
7. That’s the first half of the splice created.
8. Strip the second wire and insert it into the other end of the terminal.
9. Now crimp the second half of the splice.
10. With both halves crimped, check the joint – if you can pull the wires out you’ll need to remake the joint.
11. If you’re using a heat shrink-type crimp, shrink the tube with a hot air gun.
12. The finished splice – secure and well protected for the marine environment.
1. Cut the cable to length using heavy-duty wire shears.
2. Remove just sufficient insulation using a craft knife (taking great care not to cut or damage any of the conductors)…
3… so that the bared wire is the same length as the terminal’s collar.
3a. Insert the bared wire into the terminal.
4. Take the heavy-duty crimping tool, adjusting the size as necessary for the gauge of the terminal and cable.
5. Place the terminal in the vice and line it up with the vice jaws.
6. Fully close the vice (having adjusted it earlier it will exert the correct amount of pressure)…
7… to create the crimped terminal.
8. Cut the correct length of adhesive heat-shrink tubing and place this over the joint.
9. Heat the heat shrink tubing with a hot air gun until it has shrunk and made a tight fit over the joint.
10. The finished joint – you can just see some of the sealing adhesive visible at each end of the tubing
The third edition of Essential Boat Electrics (Fernhurst Books, £16.99) is available at fernhurstbooks.com.
Written by Oliver Ballam and the late Pat Manley, it’s a practical guide – with simple language and clear diagrams – to allow owners to tackle electrical jobs on board.
There are tutorials, from wiring a circuit, understanding switches and relays to troubleshooting electrical faults, all using easy-to-follow photo sequences.
The book also looks at tasks such as choosing solar panels and batteries and connecting navigational instruments.
Buy Essential Boat Electrics from Amazon (UK)
Buy Essential Boat Electrics from Amazon (US)
Buy Essential Boat Electrics from Foyles (UK)
Buy Essential Boat Electrics from Waterstones (UK)
Buy Essential Boat Electrics from Google Play
A subscription to Practical Boat Owner magazine costs around 40% less than the cover price.
Print and digital editions are available through Magazines Direct – where you can also find the latest deals.
PBO is packed with information to help you get the most from boat ownership – whether sail or power.
Follow us on Facebook, Instagram and Twitter
Get every issue of PBO on Android, iPhone, iPad or desktop
Struggling for spares? Some engines from different makes are the same...
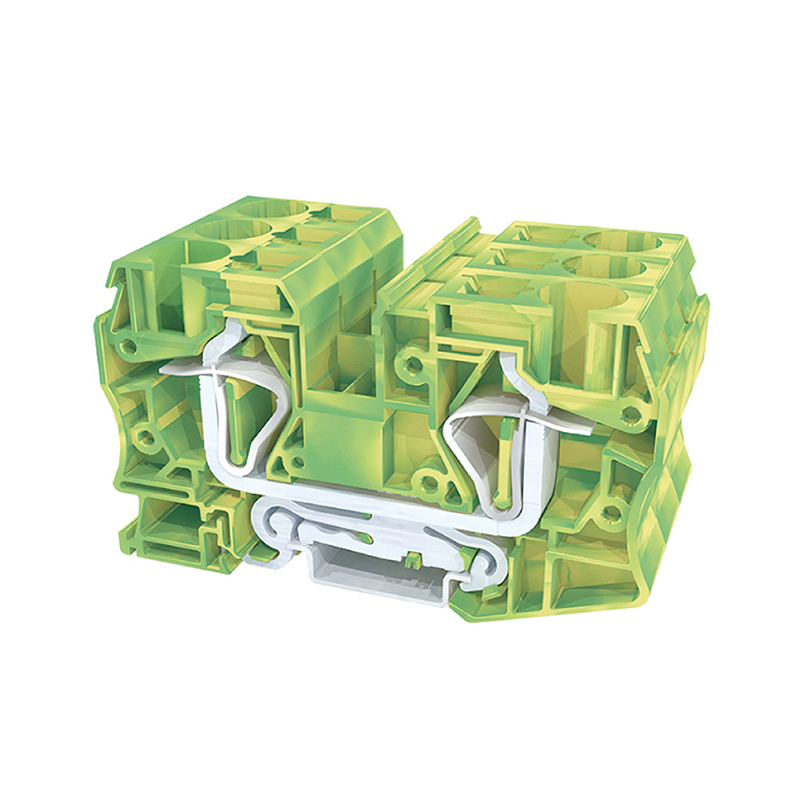
End Terminal Block The kit you shouldn't sail offshore without, the right boat insurance for you, how to manage E5 & E10 petrol, the best used boats for families, a step by step guide to make a low friction ring.... and more!